TRANSMISORES ELECTRÓNICOS
(creditos…sin duda todos para el libro de antonio creuss instrumentación industrial)
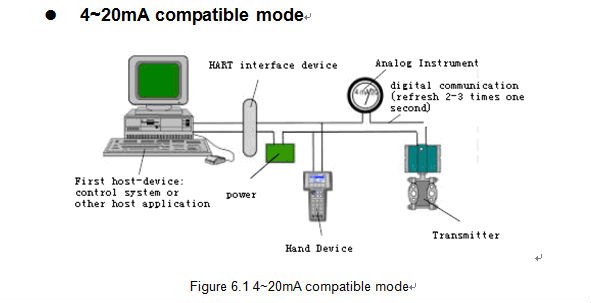
https://is.alicdn.com/img/pb/870/157/452/452157870_625.jpg imagen tomada del enlace anterior
Se puede decir que todas las variables que encontramos en los procesos industriales por muy simples que parezcan de medir son de verdad complicadas algunas veces peligrosas y tener contacto con la misma puede ocasionarnos accidentes sino se tienen las recomendaciones de seguridad necesarias para su manejo y en cuanto a la producción esta perdería su calidad y consistencia. Los transmisores electrónicos juegan un papel muy importante en el campo de la medición y control de procesos y nuestra misión como instrumentistas, ingenieros de instrumentación es mantenerlas en su punto sin que ocurran perturbaciones y cambios bruscos en los procesos y de esta manera se pueda llegar a una falla catastrófica. La primera empresa en colocar los cimientos del diseño de estos importantes equipos para la industria fue HONEYWELL cuando en el año de 1983 presentó al mercado mundial el primer transmisor digital denominado inteligente o Smart transmitter. Lo anterior nos indica que dentro del transmisor hay incorporado una serie de funciones adicionales que se añaden a las propias de la medida exclusiva de la variable. Algo que realmente para la época significaba un gran avance en el desarrollo de instrumentos y garantizaba seguridad en los procesos y eficiencia en la producción. Obviamente todas estas tareas las controlaban microprocesadores y microcontroladores instalados en la electrónica interna del equipo.
Dentro de los modelos de transmisores inteligentes o electrónicos tenemos: el capacitivo y el de semiconductor. El primero se basa en la variación de capacidad que se produce en un condensador formado por dos placas fijas separadas y un diafragma sensible interno y unido a las mismas cuando se les aplica una presión o presión diferencial a través de dos diafragmas externos. La transmisión de la presión del proceso se realiza a través de un fluido el cual puede ser aceite que rellena el interior del condensador y será como especie de un dieléctrico. La sensibilidad del diafragma es de 0.1mm como máximo, luego un circuito conformado por un oscilador y demodulador transforma dicha variación de capacidad en señal analógica. Esta señal se convierte a digital mediante un conversor o ADC eso lo debe hacer un microcontrolador y luego pasa a otro microcontrolador o microprocesador que lo que hace es acondicionar dicha señal de 4 a 20 mA, pero realmente debe hacerlo un circuito analógico. Yo pienso que más bien el microprocesador lo monitorea. Los modelos de transmisores inteligentes que son a base de semiconductores se aprovechan de las propiedades eléctricas que tienen estos dispositivos cuando se les aplica un voltaje. El modelo de semiconductor difundido está fabricado a partir de una delgada película de silicio y usa técnicas de dopado para generar una zona sensible a esfuerzos y deformaciones. Se comporta como un circuito continuo de puente de wheastone aplicable a la medida de presión, presión diferencial y nivel formado por una pastilla de silicio difundido en el que se hallan embebidas o acopladas unas serie de resistencias que en este caso son 4 Ra, Rb, Rc, Rd de un puente de wheatstone. El desequilibrio del puente originado por cambios en la variable da lugar a una señal de salida de 4 a 20 mA, su funcionamiento es el siguiente: cuando no existe presión los voltajes V1 y V2 son iguales y al aplicar presión de proceso, las resistencias Rc y Rd disminuyen su resistencia, Ra y Rd la aumentan dando lugar a caídas de tensión distintas y a una diferencia entre V1 y V2. Esta diferencia se aplica a un amplificador de alta ganancia que controla un regulador de corriente variable. Un margen de corriente contínua de 3 a 19 mA con 1 mA de puente produce una señal de salida de 4 a 20 mA . Esta corriente circula a través de la resistencia de realimentación Rfb y eleva a V1 el voltaje equivalente a V2 y le da equilibrio al puente. Como la caída de tensión producida a través de Rfb es proporcional a R2b esta resistencia fija el intervalo de medida span del transductor. El cero del instrumento se varia intercalando resistencias fijas en el brazo izquierdo del puente y un potenciómetro en el brazo derecho. Normalmente la pastilla de silicio contiene dos puentes de wheastone uno de presión y otro de presión diferencial y una termorresistencia. El microprocesador compensa las no linealidades de los elementos o sensores individuales, convierte las tres señales analógicas o impulsos y calcula mediante datos prefijados en fábrica y almacenados en su memoria un valor digital de salida que es transformado a la señal analógica de 4-20 mA. Un comunicador portátil de teclado alfanumérico que puede conectarse en cualquier punto del cable de dos hilos entre el transmisor y el receptor permite leer los valores del proceso, configurar el transmisor, cambiar su campo de medida y diagnosticar averias.
El instrumento proporciona un aumento en la precisión de la señal transmitida y en la precisión del lazo de control del orden del 0.15% y lo que es más importante, unas posibilidades de calibración y cambio del margen de medida no conocidas hasta entonces. Antes de su aparición, la calibración y el cambio del margen de medida no conocidas hasta entonces. Antes de su aparición, la calibración y el cambio del margen de medida debían realizarse normalmente en el taller de instrumentos lo que equivalía a disponer de aparatos de repuesto para continuar trabajando con el proceso, siendo inevitable la marcha a ciegas durante el tiempo requerido para el cambio mecánico del instrumento. Por ejemplo la calibración del instrumento de nivel típico requiere el vaciado del tanque, el desmontaje del aparato y su calibración. Además si se precisa que el proceso continue en funcionamiento es necesario montar una brida ciega en la brida del transmisor de nivel para poder llenar el tanque y continuar las operaciones de fabricación.
En variables especificas tales como caudal el transmisor inteligente proporciona una mejora en la relación caudal máximo/ caudal mínimo que pasa de 3:1 en la placa orificio ( o tobera o tubo venturi) 10:1 manteniendo la misma precisión de +_1%
Los transmisores digitales disponen de autocalibración por ejemplo. Este sistema lo dispone un transmisor de ultrasonido, disponen de un reflector de las ondas sónicas que está situado en el tanque sobre la superficie del líquido y hacia donde el emisor dirige periódicamente por ultrasonidos ajustando entonces los parámetros de calibración. De este modo compensa las variaciones de velocidad del sonido provocadas por cambios en la temperatura del ambiente del tanque. En otros casos la autocalibración es más difícil de conseguir. Tal ocurre en los medidores magnéticos de caudal en los que durante los intervalos de calibración sería necesario pasar por el elemento un caudal conocido de un determinado fluido.
Los transmisores inteligentes se presentan también al autodiagnóstico de sus partes electrónicas internas, función que proporciona el departamento de mantenimiento: primero el conocimiento de la existencia de un problema en el circuito segundo el diagnóstico y la naturaleza del problema en el circuito. Segundo el diagnostico y la naturaleza del problema señalando que el instrumento ha fallado y tercero las líneas a seguir para la reparación o sustitución del instrumento.
Con la entrada del transmisor inteligente, la calibración y el cambio de margen de trabajo se logran simplemente por examen de los datos almacenados en una PROM y por utilización de técnicas digitales. Se consigue de este modo una relación turndown (máximo vs mínimo de la variable) cuyo valor máximo es de 4000:1 frente a la relación 1-6 de un transmisor de presión o nivel convencional, lo que posibilita a la reducción drástica del número de transmisores en stock al poder utilizar prácticamente un solo modelo para cubrir los diferentes campos de medida utilizados hasta entonces en fábrica. A señalar que si el campo de medida SPAN es pequeño, se pierde precisión. La señal de salida continua siendo 4-20 mA pero honeywell en la década de los 80s presentó ya el transmisor con señal de salida enteramente digital lo que proporciona un aumento en la precisión del lazo de control que pasa al 0.15% al eliminar los conversores analógicos digital A/D del transmisor y los conversores de digital analógico D/A del receptor. (indicador, registrador, controlador) en líneas generales la precisión total del lazo de control utilizando transmisores convencionales es del 0.84% empleando transmisores inteligentes es de 0,29% y usando transmisores digitales inteligentes pasa al 0.15% y si estos últimos incorporan un algoritmo de caracterización mejoran todavía más la precisión del lazo llegando a 0.075% otras ventajas adicionales de estos transmisores son el cambio automático del campo de medida, caso de que el valor de la variable salga del campo, rutinas de autodiagnóstico, monitoreo de temperaturas y tensiones de referencia de los transmisores, la fijación de la variable en el ultimo valor alcanzado, en caso de detectarse alguna irregularidad en el funcionamiento del aparato, el autoajuste desde el panel de control, la función de caracterización que compensa las diferencias entre las condiciones de calibración en fábrica y las condiciones de campo actuales y que permite la instalación directa en campo y la fijación del campo de medida sin calibración, etc. Para visualizar la señal de salida, los datos de configuración, el margen de funcionamiento, y otros parámetros y cambiar ajustes del campo de medida se utiliza un comunicador portátil que se conecta en cualquier punto de la línea de transmisión.
BIBLIOGRAFÍA-
instrumentación industrial-antonio creuss solé editorial marcombo 2005 775 paginas.
CONTENIDOS MÁS RELEVANTES.